How Heat Transforms Coatings in Industrial Curing Ovens
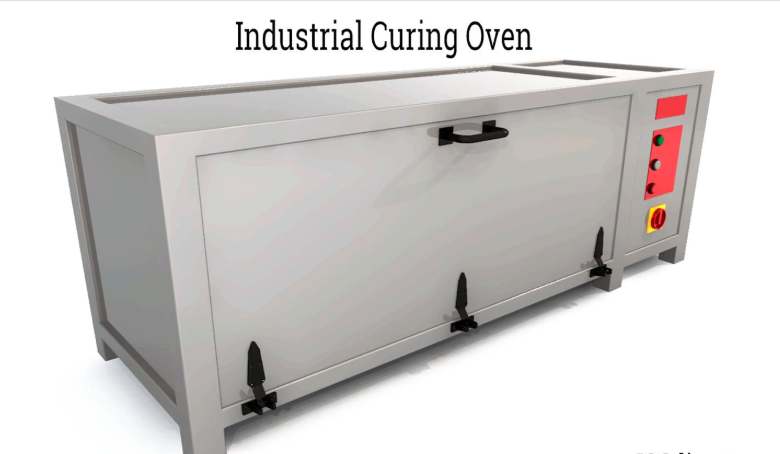
Anyone who’s ever worked with industrial coatings knows that the magic happens when heat meets material. This powerful combination is the driving force behind durable, long-lasting finishes. Understanding how an industrial curing oven works is key to achieving the perfect coating every time, and it’s all about harnessing heat to alter the material on a molecular level. Let’s dive into how exactly heat transforms coatings into tough, protective layers.
The Science Behind Powder Melting Into a Smooth, Durable Finish
In an industrial powder coating oven, heat isn’t just about making things hot—it’s about creating the right conditions for the powder to transform. Powder coating begins as a dry, finely ground material. Once it’s applied to the object, the industrial curing oven heats the surface, causing the powder to melt. But this process doesn’t end with a mere coating—it’s the beginning of a molecular change that will result in a smooth, hard finish.
As the heat gradually builds, the powder particles start to soften and flow together, eventually forming a smooth, uniform layer on the surface. This is where the magic of durability begins. The melting powder isn’t just forming a thick shell; it’s undergoing a chemical transformation. The resin in the powder begins to crosslink, hardening into a solid, protective surface. This process creates a long-lasting finish that’s resistant to scratches, corrosion, and fading, which is why the precise heat in an industrial powder coating oven is so critical.
How Precise Heat Levels Strengthen Coatings for Long-Term Performance
Heat control is everything when it comes to curing coatings. An industrial curing oven works by providing consistent and precise temperature levels that allow coatings to reach their full potential. Too much heat and the coating can blister or burn; too little, and it won’t cure properly, leaving the finish brittle and prone to damage. The key is maintaining the right temperature profile for the specific coating material.
This precision isn’t just for aesthetics—it directly affects the strength and longevity of the coating. When the heat is applied at the correct level, the molecules in the coating material bond in a way that creates a tough, resilient layer. The result is a finish that can withstand physical wear, extreme temperatures, and exposure to chemicals. In industrial settings, where equipment and materials are subject to harsh environments, having this reliable, tough coating ensures the product lasts for years to come.
Read also: How Remote Medical Scribes Are Revolutionizing Patient Care
The Role of Air Circulation in Achieving Even and Consistent Curing
Air circulation in an industrial curing oven plays a huge role in making sure the heat is evenly distributed. Without proper airflow, certain areas of the coating may not cure properly, leading to uneven results. This is why high-quality industrial ovens are designed with advanced circulation systems that ensure the heat reaches every inch of the surface being coated.
Good air circulation is also key to preventing overheating. When heat is evenly distributed, the coating can cure uniformly, which is essential for both appearance and functionality. If one part of the object overheats, the coating may begin to burn or degrade, affecting the overall finish. Consistent airflow makes sure the heat is not only effective but also efficient, creating a high-quality result every time.
What Happens at the Molecular Level When Coatings Are Exposed to Heat?
At the molecular level, the magic happens during the curing process. When coatings are heated in an industrial curing oven, the heat excites the molecules, causing them to move and interact in new ways. For powder coatings, this process triggers the resins and hardeners to react, forming crosslinks that make the coating stronger and more durable.
Essentially, heat causes the coating material to “set” into its final, hardened form. The molecules bond together, creating a dense, tough surface that provides superior protection. This transformation is what makes heat treatment so powerful—it takes a relatively fragile substance and turns it into a highly durable coating. Understanding this molecular change is key for manufacturers who rely on industrial ovens to create high-quality products.
The Transition from Liquid to Solid That Creates a Tough Protective Layer
When you’re dealing with coatings, the transition from liquid to solid is where the real strength of the finish is formed. In the case of liquid coatings, heat helps them to cure and harden, but in the case of powder coatings, this transition happens in stages. Initially, the powder coating is a dry, free-flowing material, but as the heat increases, the powder begins to melt into a liquid-like state, before chemically bonding and turning into a solid.
This transformation is critical for the final appearance and durability of the coating. The liquid phase allows the coating to flow smoothly across the surface, eliminating imperfections and filling in minor gaps. Once solidified, the coating becomes a tough, impermeable layer that resists scratches, stains, and corrosion. This heat-driven transition is one of the most essential stages in ensuring the final product meets industrial standards.
Why Controlled Cooling After Curing Is Just as Important as the Heating Process
Cooling may seem like the final, passive step, but it’s just as important as heating. When coatings are exposed to heat in an industrial curing oven, they expand and soften, but they need to cool at a controlled rate to set properly. If the cooling process is too rapid, it can cause the coating to crack or warp. Controlled cooling ensures that the molecular bonds in the coating form properly, leading to a durable, even finish.
This cooling phase is where the coating solidifies completely and reaches its full strength. Rapid or uneven cooling can stress the coating and result in defects, which is why many industrial curing ovens feature built-in cooling zones. These zones allow for a gradual reduction in temperature, ensuring that the coating hardens evenly and maintains its strength.
How Different Coating Formulations React to Varying Temperature Profiles
Not all coatings react the same way to heat. Different formulations require different temperature profiles to achieve the best results. For example, some coatings cure at lower temperatures, while others require much higher temperatures to properly bond. In an industrial curing oven, it’s important to adjust the temperature settings based on the type of coating being used.
A powder coating might need a higher temperature for a short period, while liquid coatings may require a longer curing time at lower temperatures. Understanding these differences is essential for manufacturers to get the best results. An oven designed with customizable temperature controls can help ensure that each coating type gets the precise treatment it needs for maximum performance and durability.